Grit Removal System
The Compact Grit Removal System (Product ID: ICR) offers the same benefits as the Screen and Grit Removal Package (Product ID: ICE) but does not include any screening. The Compact Grit Removal System is a primary treatment machine is designed to provide grit removal pre-treatment in a single packaged unit process. Influent passes through a longitudinal sedimentation tank, where heavy particles (sand and grit) settle to the bottom. Sand and grit are removed from the sedimentation tank via a system of screws.
A horizontal shaftless grit conveying screw transports settled grit to the sump. Grit is then removed from the sump via a shafted extraction screw which lifts the grit from the tank for discharge into a bin. A blower can be installed as an option in the sedimentation tank to assist with fluidising the settled sand and grit, for easier removal by the extraction screw. This compact system can also be configured to remove fats, oils and grease as an added option.
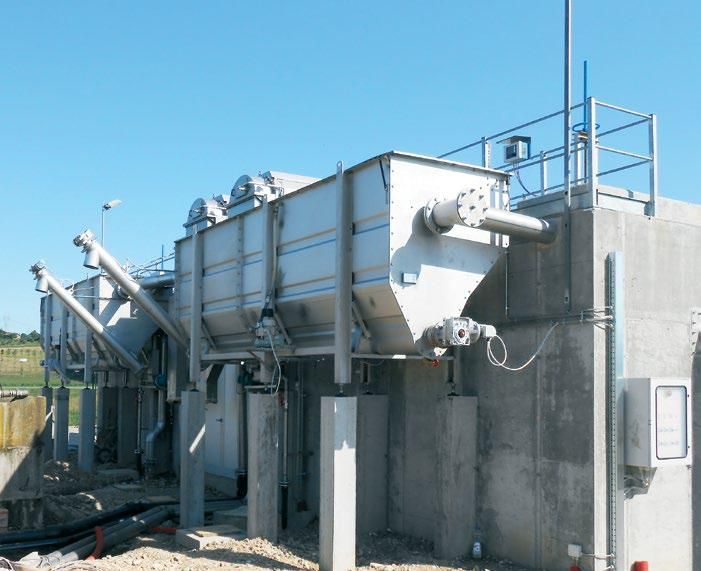
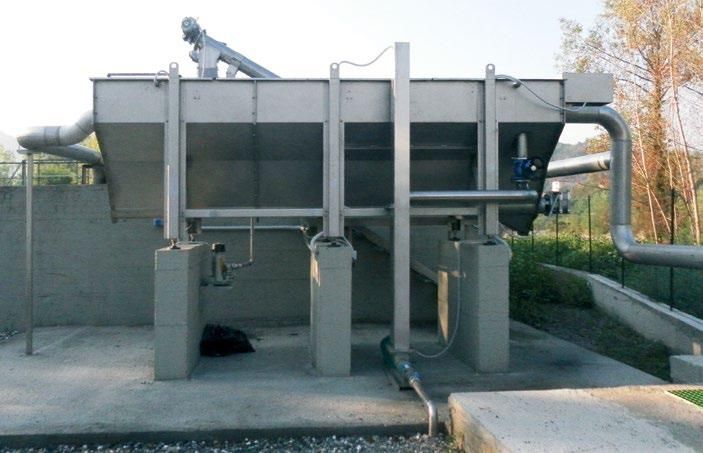
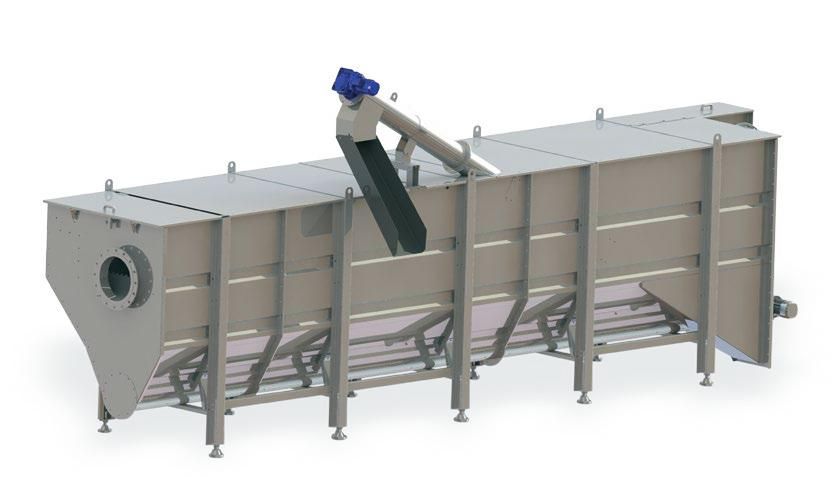
Using the influent TSS 500 mg/L with up to 0.5% grit as basis for the design reference, the typical performance of the ICrs has up to 90% removal efficiency for grit particles > 200 µm. The ICrs is available in various treatment capacities ranging from 10 to 150 L/s.
Applications
Real-world examples
Grit Removal for Truck Wash
A large truck washing company was having problems with sludge accumulation in its source water pits that it was using for vehicle wash-down. This sludge accumulation was so high that it was reducing its water storage capacity and thus impacting on operations. MAK Water was asked to review the operation and recommend a long-term solution that reduced its ongoing costs whilst resolving its current water storage issues.
Bunbury, Western Australia
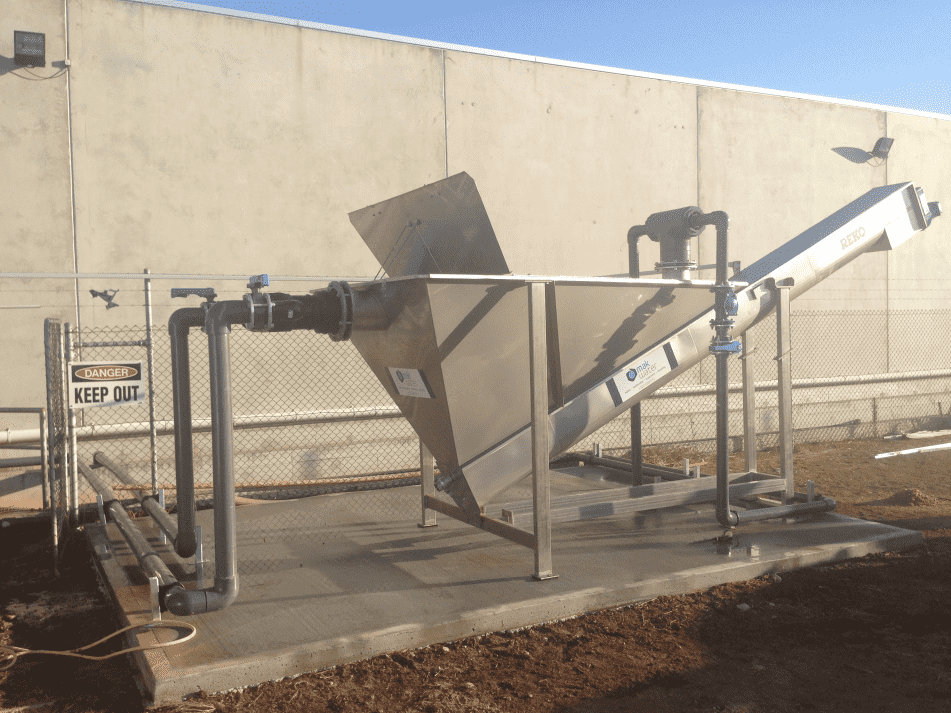
Screening & Grit Handling
Related Solutions
Compact Screen and Grit Removal Package
The Compact Screen and Grit Removal Package (Product ID: ICE) is a primary treatment machine that combines screening and grit removal in a single compact plant.
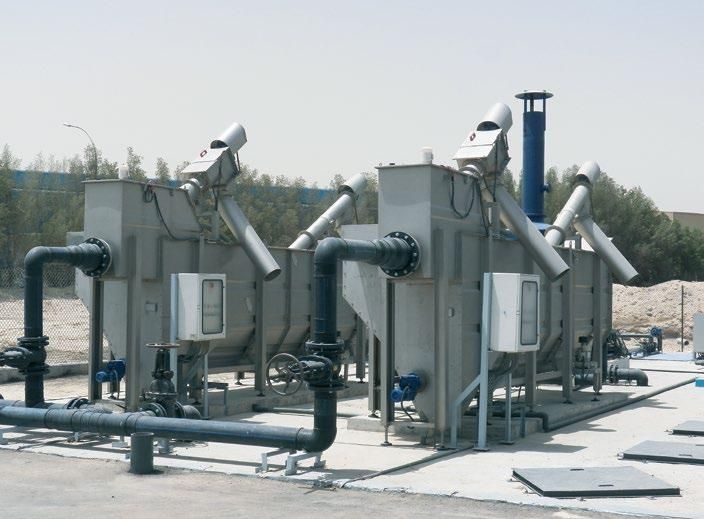
Compact Screw Screen
The Compact Screw Screen (Product ID: SSG) is an economical solution for screening of industrial wastewater or domestic sewage.
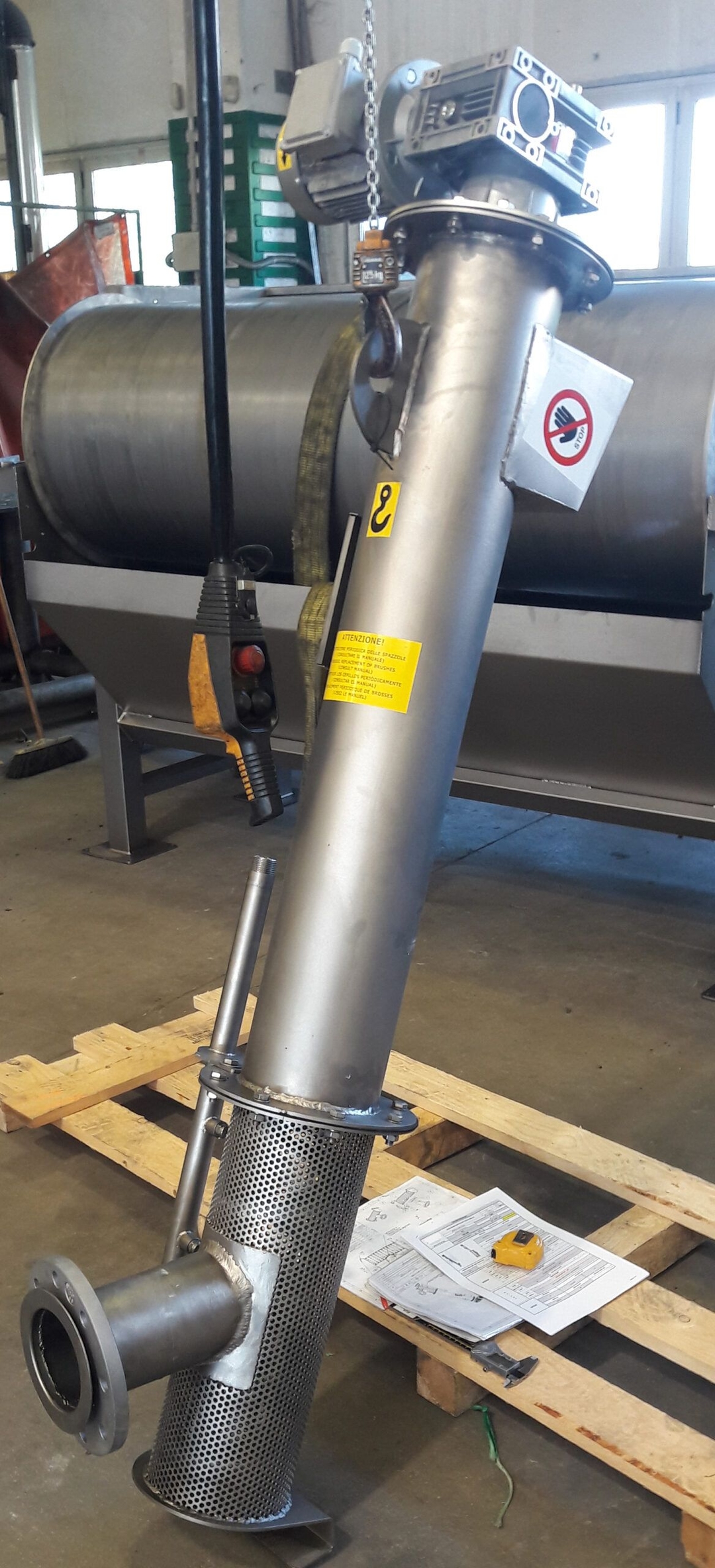
Grit Classifier
MAK Water’s Grit Classifier (Product ID: SAK) is used to separate grit (which can contain sand, gravel and other heavy solids) from municipal and industrial wastewater streams.
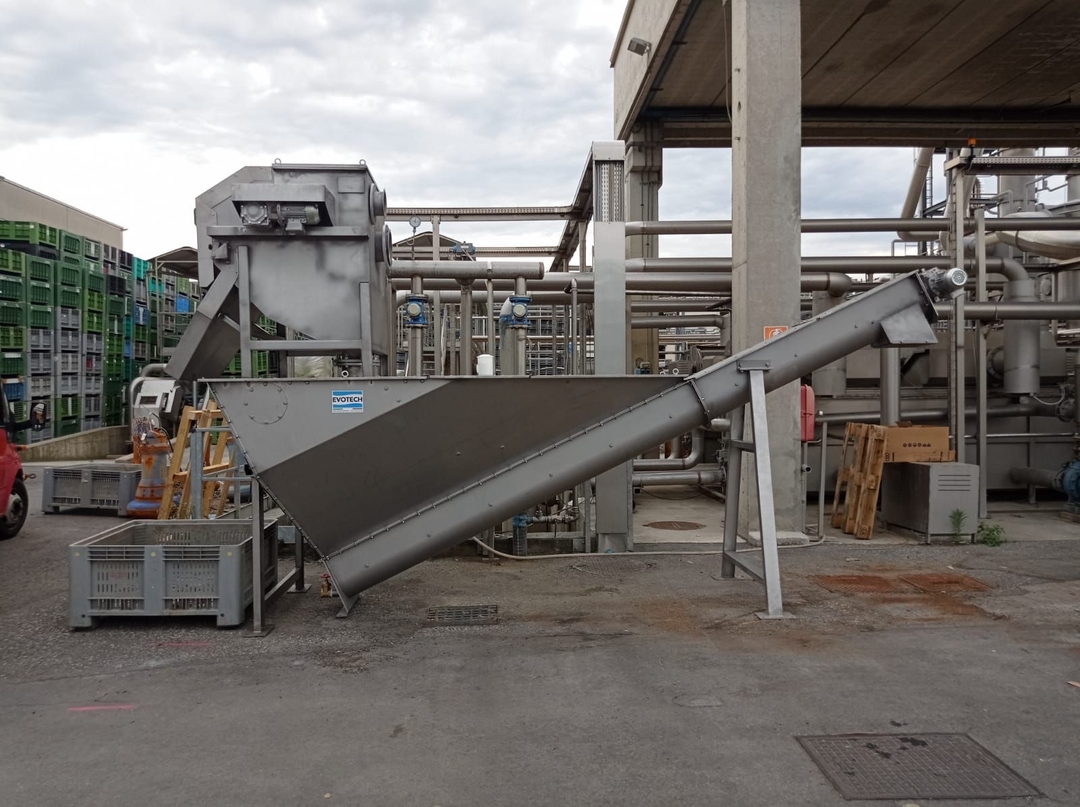
Internally Fed Drum Screen
The Internally Fed Drum Screen is a free-standing unit designed for separating settling solids from wastewater using an internally fed rotating drum screen.
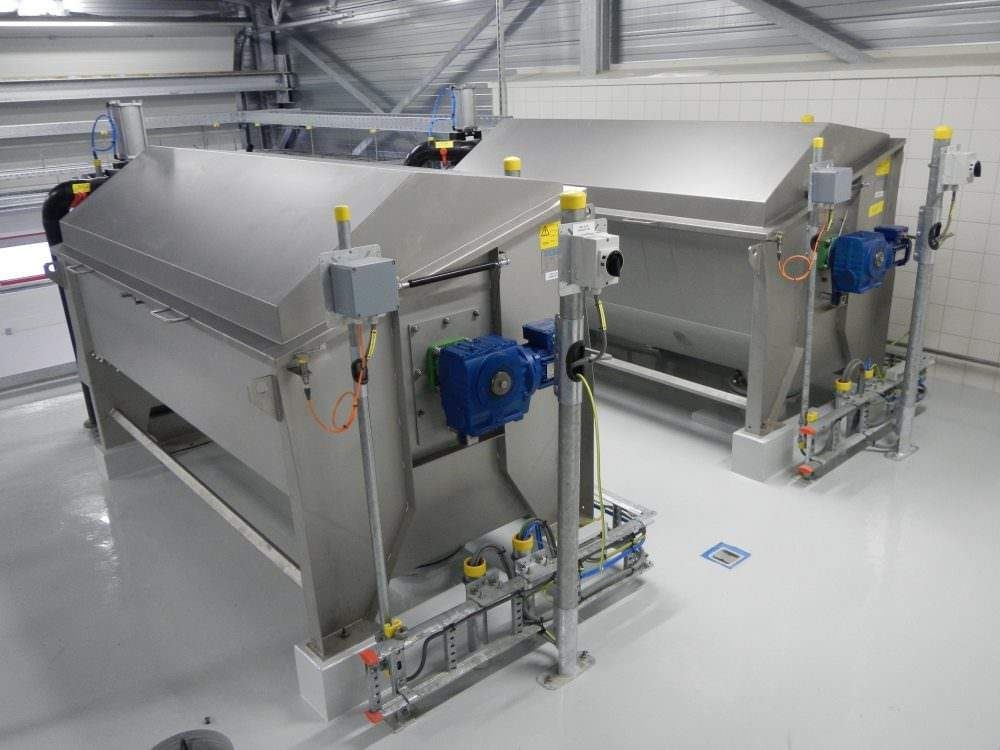
Rotary Drum Screen
The Rotary Drum Screen (Product ID: FTR) is designed to remove solids from industrial wastewater streams.
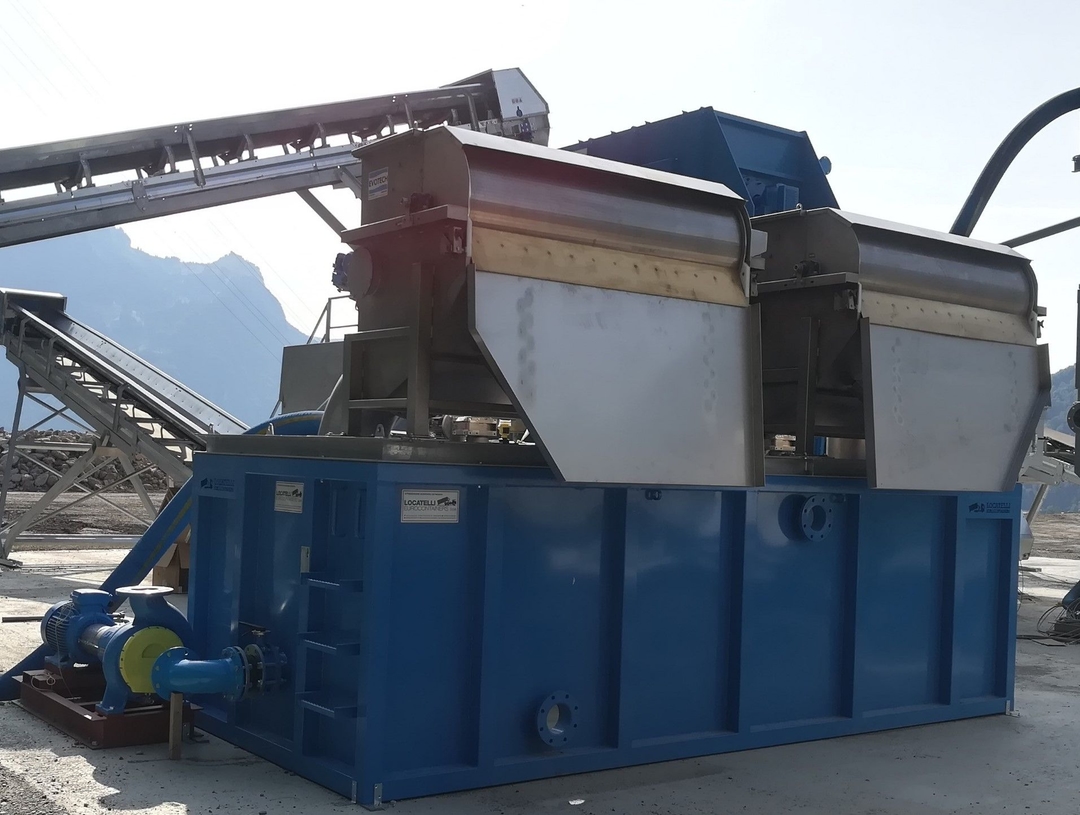
Rotating Drum Screw Screen
The Rotating Drum Screw Screen with integrated screenings compaction (Product ID: SSTF) offers exceptional efficiency in removing floating and suspended solids from municipal and industrial wastewater.
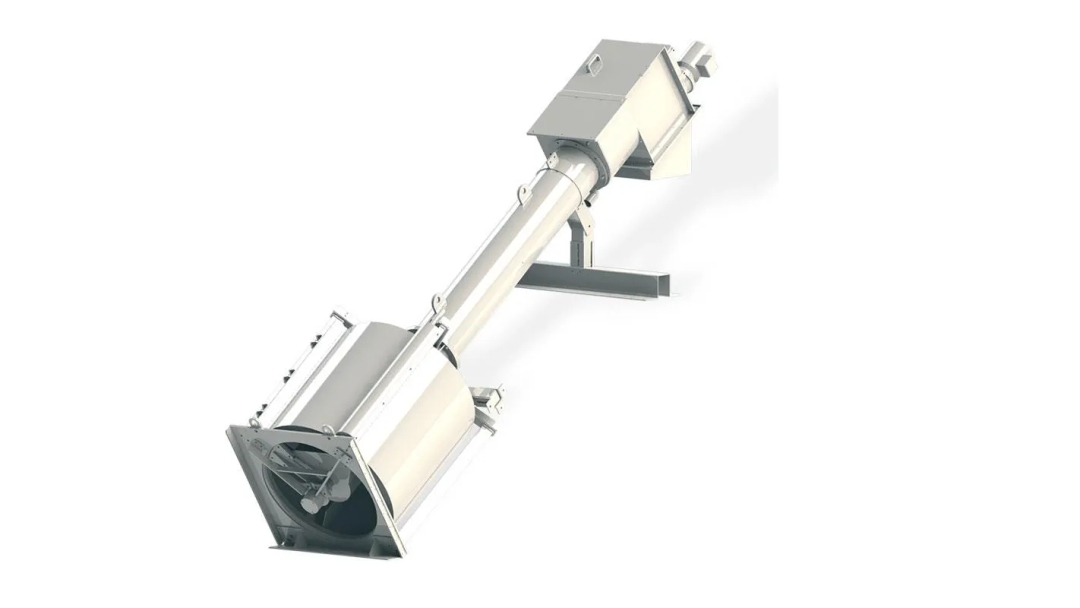