Technology Overview
How WendeWolf® Solar Sludge Drying Works
The WendeWolf® system transforms dewatered sludge cake into a dry, granulated product using solar energy. Installed inside an enclosed greenhouse, it prevents re-wetting and enhances evaporation. A tiller and turner mechanism spreads, aerates, and transports sludge along the drying hall, reducing moisture content to up to 85% dry solids.
A typical WendeWolf® facility includes the automated tiller and turner machine, a greenhouse drying hall (configured as standalone or multiple halls), ventilation fans, meteorology instruments, and an automated control system.
The system can operate in Batch mode or Continuous mode without changing the programming. It turns over and conveys the sludge homogeneously in one single process along the full width and length of the hall. It does not touch the floor and therefore does not damage the floor. At start-up the WendeWolf® machine’s on-board sensors are used to “map” the floor surface. This process determines the minimum operating height from the floor across the width and length of the hall.
- Handles dewatered cake input piles up to 110 cm high.
- Operates (Turning and Displacing) a sludge bed depth up to 40 cm.
- Can stockpile the dried granulate product up to 80 cm high.
- Uses robust, low wear, easy to maintain, and exchangeable tilling tools.
Key Features
Control system adjustable programmes to allow for automated operation
- Loading – import and flatten input piles of sludge into the hall, and to spread it across the width of the hall, over a selected length in the hall.
- Turning – turn over the drying sludge for a selected sludge bed depth, over a selected length in the hall. Turning can occur in both directions; there is no preferred direction.
- Displacing – move the sludge for a selected sludge bed depth, over a selected length in the hall. Displacing can occur in both directions.
- Accumulating – accumulate or stockpile dried granulate product
- Clearing – remove dried granulate product from the end of hall, where an automated out-loading system is available
Key Process Features
- Sludge input Dewatered sludge cake (≥13% dry solids) is loaded manually or via automatic conveyors into the drying hall
- Drying process Solar radiation and controlled ventilation drive moisture from the dewatered sludge through evaporation, assisted by the WendeWolf machine’s automated turning and aeration.
- Granulate output Dried sludge is discharged in granular form suitable for agriculture, fuel production, or landfill diversion.
- Reduced transport costs Drying from 15% to 85% dry solids cuts sludge mass by 78%, significantly lowering disposal costs.
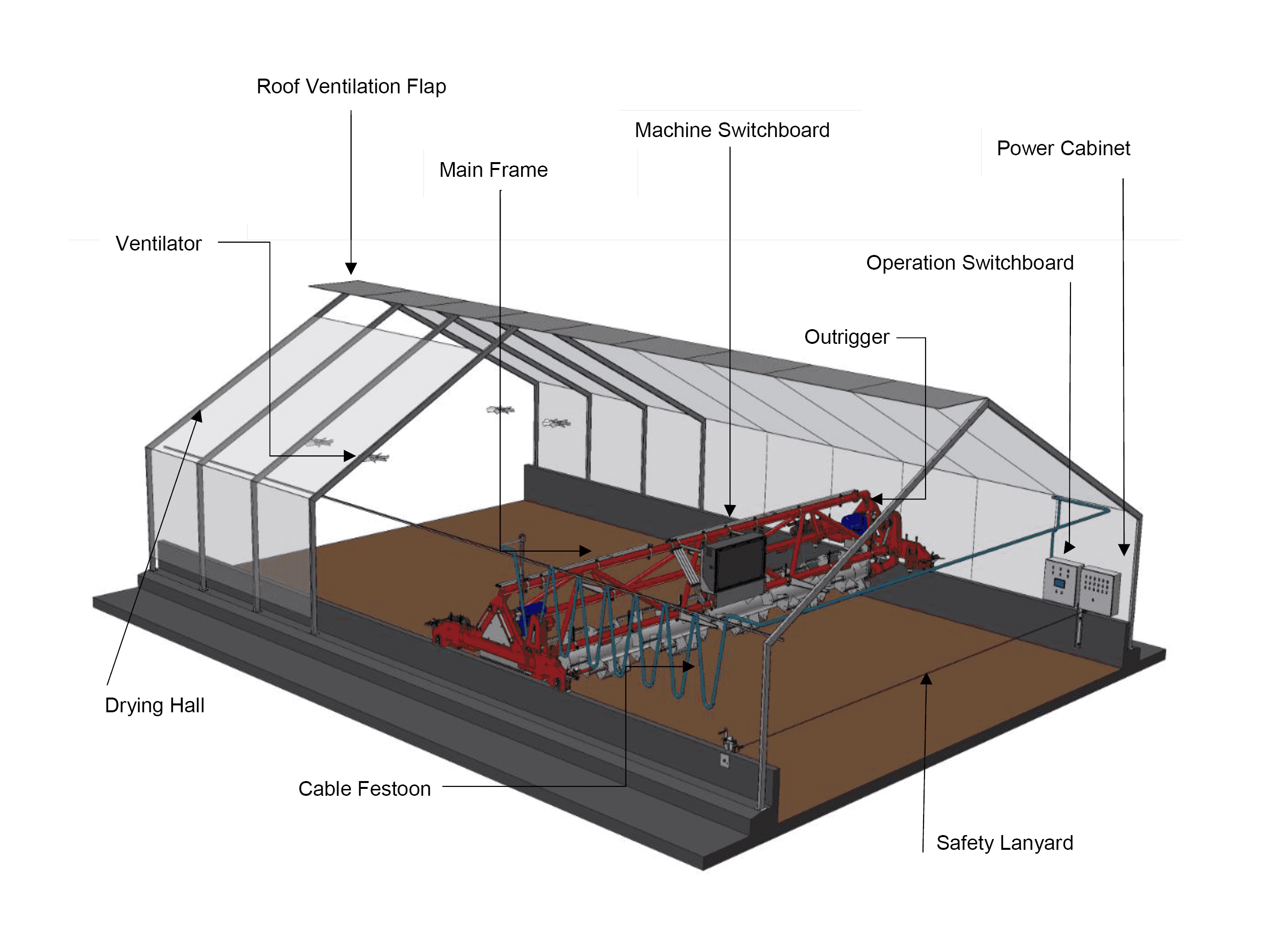
Disclaimer: We continuously update and improve our products and services, contact us for more detailed information or to confirm specifications. MAK Water takes no responsibility for any errors resulting from the use of information contained on this website.
Sludge Handling