Dissolved Air Flotation
The MAK Water Dissolved Air Flotation (DAF) system is a superior counter current system designed to achieve maximum treatment efficiency in a compact footprint. It is able to remove a variety of contaminants to meet trade waste or reuse requirements. Each system is sized based on the hydraulic loading rate, Total Suspended Solids (TSS) and Fats, Oil and Greases (FOG) levels. The surface loading rate that can be applied is dependent on each application.
The DAF separates the suspended solids and lighter liquid contaminants (e.g. FOG and hydrocarbons) from the water by moving them to the surface of the DAF vessel and then scraping them off the surface. A pressurised stream of airsaturated water is mixed with the flocculated water and with the release of pressure, a cloud of very fine air bubbles carries the suspended solids and lighter liquids to the tank surface. Clean water overflows from the DAF tank, via an under/over-weir to sewer or to the next stage of the treatment process. The overflow level is adjustable and controls the level in the DAF flotation section. The sludge on the surface of the DAF is scraped into a sludge hopper by a mechanical scraper. The DAF system is automated via a programmable logic controller (PLC) mounted within a control cabinet on the system.
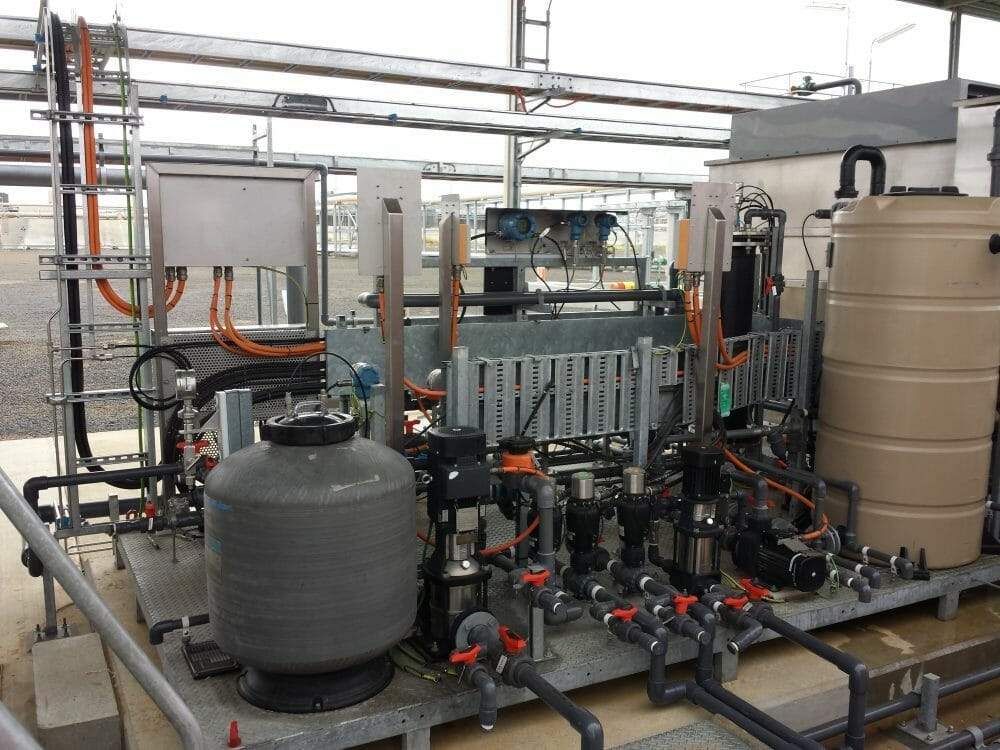
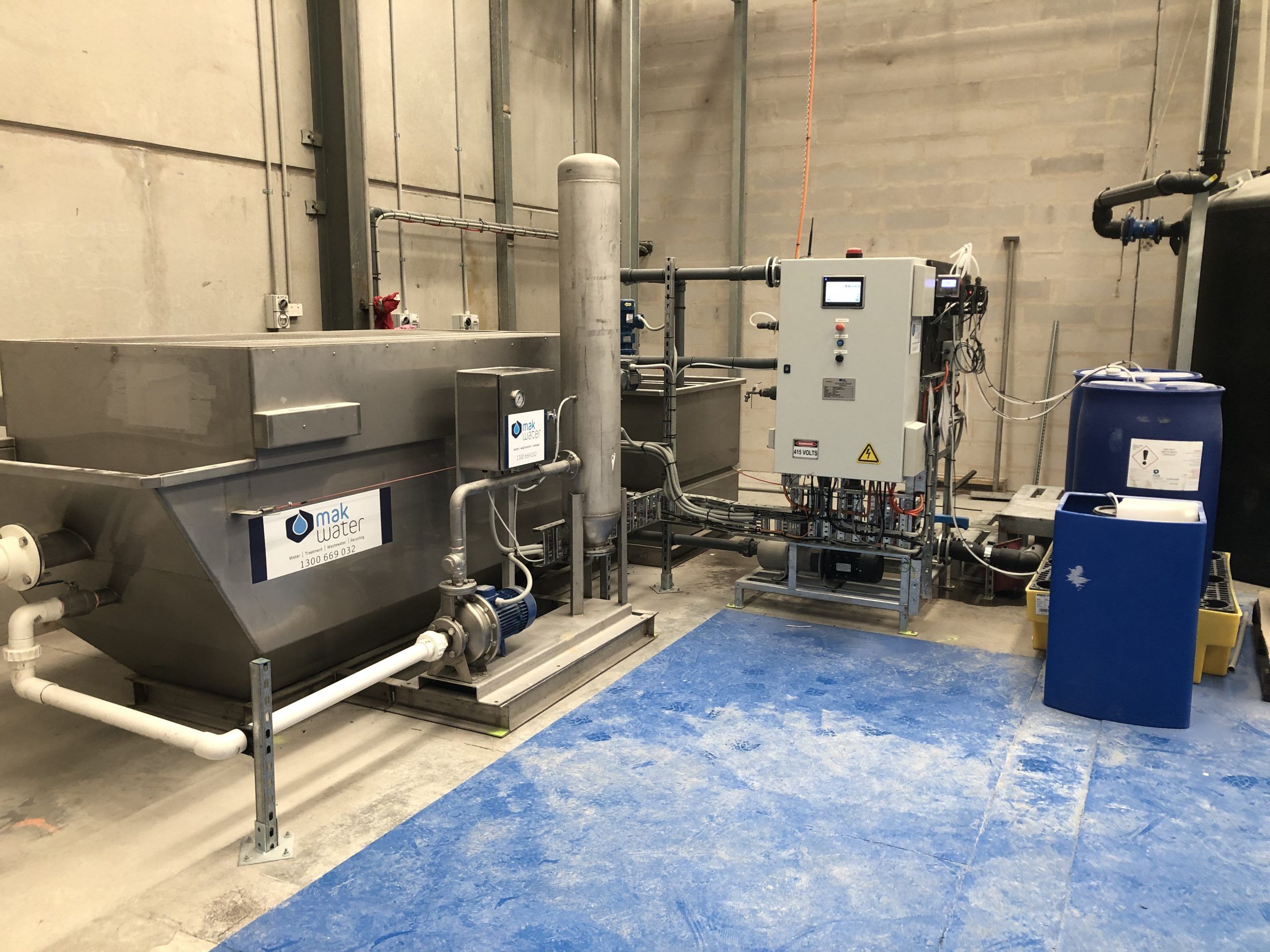
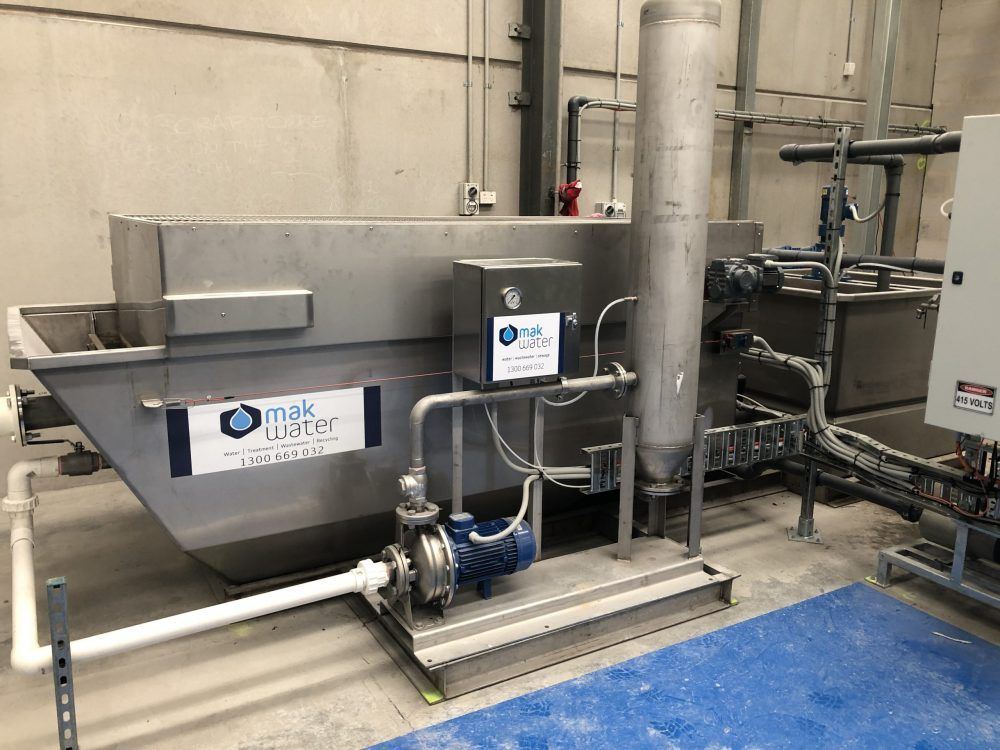
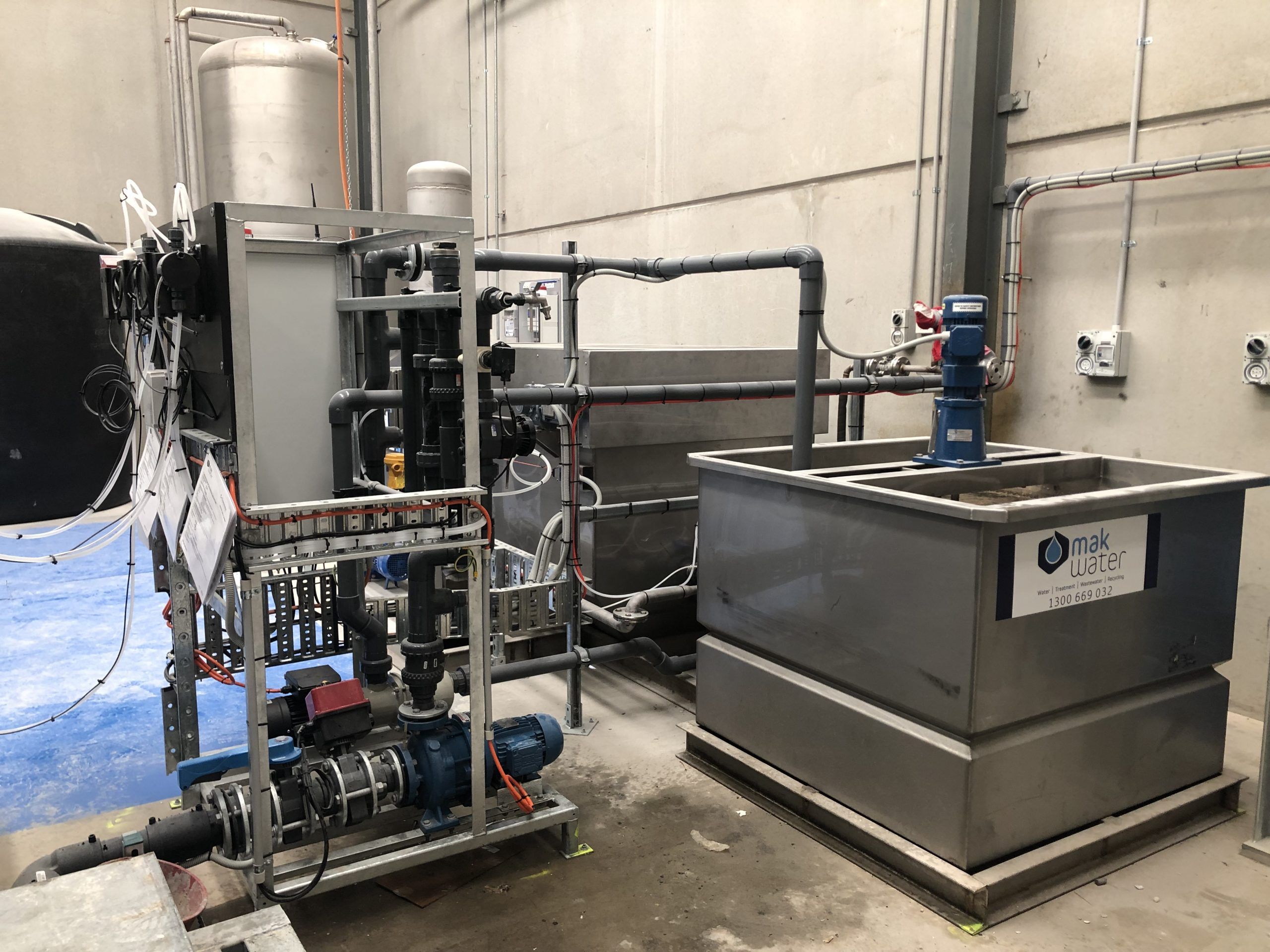
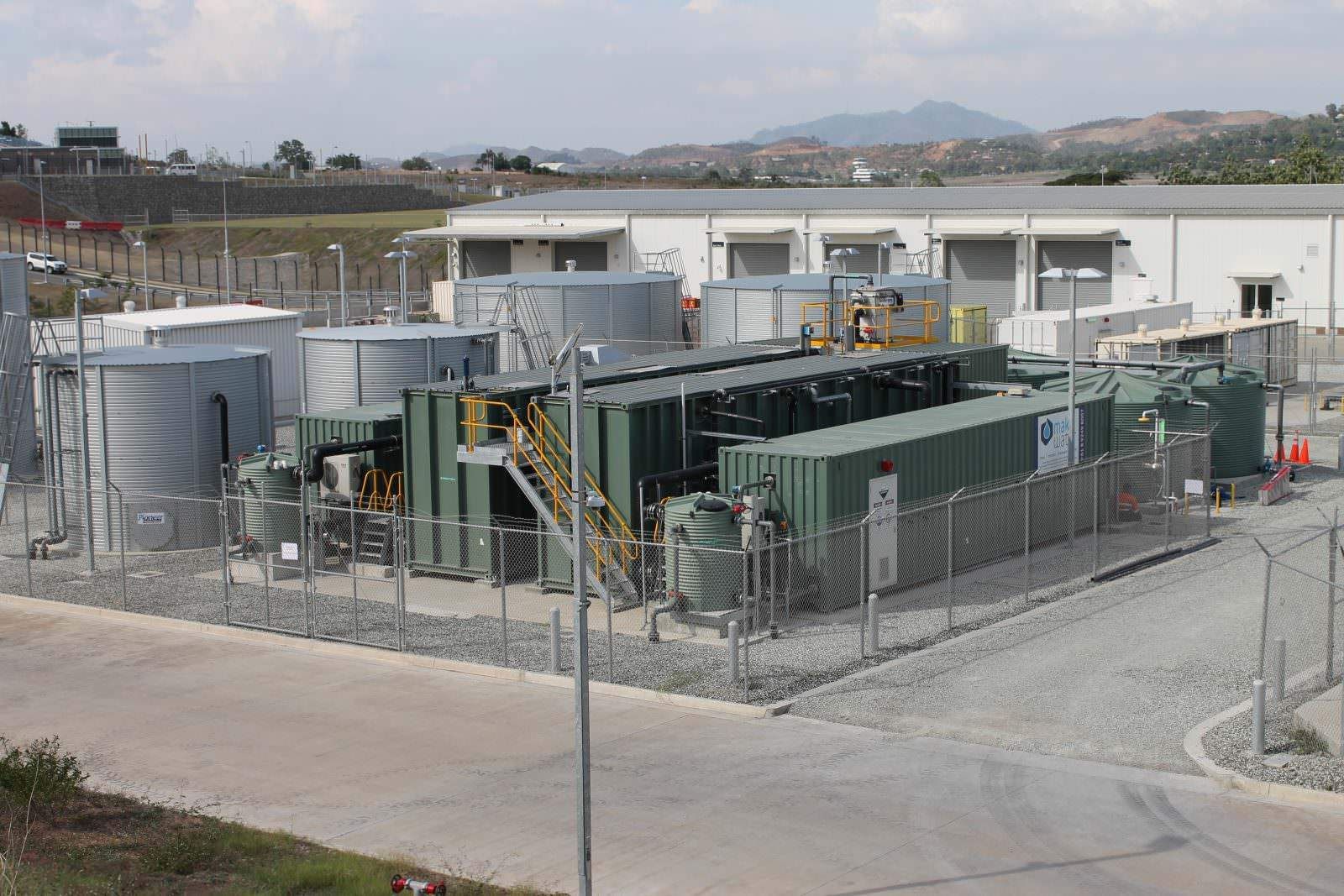
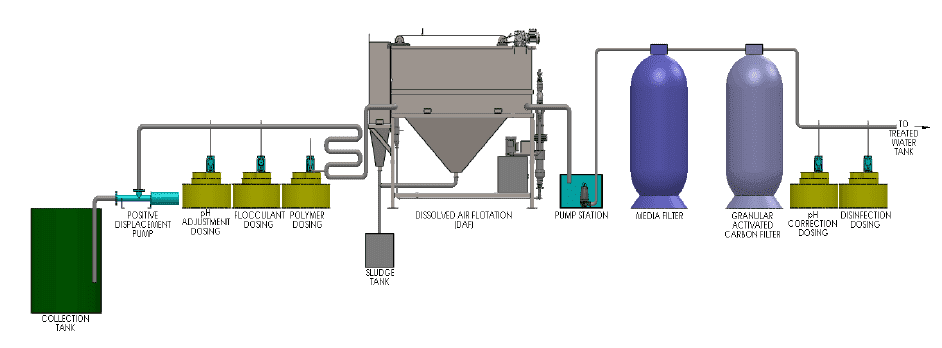
Technical Specifications
Standard Specifications
Parameter | Units | DAF 1.0 | DAF 1.5 | DAF 3.5 | DAF 10 | DAF 20 | DAF50 | DAF100 | DAF200 | ||||||||||||||||||
---|---|---|---|---|---|---|---|---|---|---|---|---|---|---|---|---|---|---|---|---|---|---|---|---|---|---|---|
DAF Flow Rate | m3/hr | 1.0 | 1.5 | 3.5 | 10 | 20 | 50 | 100 | 200 | ||||||||||||||||||
Total Inlet Solids | mg/L | 10,000 | |||||||||||||||||||||||||
FOG Removal | % | 85~95 (Application Dependent) | |||||||||||||||||||||||||
TSS Removal | % | 70~99 (Application Dependent) | |||||||||||||||||||||||||
COD Removal | % | 20~80 (Application Dependent) | |||||||||||||||||||||||||
BOD Removal | % | 20~80 (Application Dependent) | |||||||||||||||||||||||||
Power Consumption | kW | 2 | 3 | 4 | 7 | 12 | 25 | 44 | 84 | ||||||||||||||||||
Footprint | m | 2.2 x 2.0 | 2.2 x 2.0 | 3.0 x 2.5 | 4.0 x 3.0 | 4.0 x 3.0 | 6.0 x 5.0 | 9.0 x 5.0 | 10.0 x 6.0 |
Standard Inclusions and Options
Equipment | DAF1.0 | DAF1.5 | DAF3.5 | DAF10 | DAF20 | DAF50 | DAF100 | DAF200 | |||||||||||||||||||
---|---|---|---|---|---|---|---|---|---|---|---|---|---|---|---|---|---|---|---|---|---|---|---|---|---|---|---|
Skid Mounted Plant & Equipment | ✓ | ✓ | ✓ | ✓ | ✓ | - | - | - | |||||||||||||||||||
Feed Pump | Standard | ✓ | ✓ | ✓ | ✓ | ✓ | ✓ | ✓ | ✓ | ||||||||||||||||||
Submersible | o | o | o | o | o | o | o | o | |||||||||||||||||||
Pre-Treatment | Flocculent Dosing | o | o | o | o | o | o | o | o | ||||||||||||||||||
Polymer Dosing | o | o | o | o | o | o | o | o | |||||||||||||||||||
pH Adjustment | o | o | o | o | o | o | o | o | |||||||||||||||||||
PLC Control System with HMI | ✓ | ✓ | ✓ | ✓ | ✓ | ✓ | ✓ | ✓ | |||||||||||||||||||
On Board Air Compressor | o | o | o | o | o | o | o | o | |||||||||||||||||||
Treated Water Recycling for Saturator | o | o | o | o | o | o | o | o | |||||||||||||||||||
Saturator Feed - Potable Water Top Up | o | o | o | o | o | o | o | o | |||||||||||||||||||
Flow Based Chemical Dosing | o | o | o | o | o | o | o | o | |||||||||||||||||||
Containerised System, c/w A/C & Lights | o | o | o | o | - | - | - | - | |||||||||||||||||||
Container Insulation (walls & ceiling) | o | o | o | o | - | - | - | - | |||||||||||||||||||
Container Non-slip Floor Coverings | o | o | o | o | - | - | - | - | |||||||||||||||||||
Container Side Access Door | o | o | o | o | - | - | - | - | |||||||||||||||||||
Additional Pre DAF Treatment | o | o | o | o | o | o | o | o | |||||||||||||||||||
Additional Post DAF Treatment | o | o | o | o | o | o | o | o | |||||||||||||||||||
Premium Instrument Package | o | o | o | o | o | o | o | o | |||||||||||||||||||
Sludge Pump | o | o | o | o | o | o | o | o |
Instrumentation | Standard Package | Premium Package | |||||||||||||||||||||||||
---|---|---|---|---|---|---|---|---|---|---|---|---|---|---|---|---|---|---|---|---|---|---|---|---|---|---|---|
Pressure Gauges | ✓ | ✓ | |||||||||||||||||||||||||
pH Transmitter (4-20mA) | ✓ | ✓ | |||||||||||||||||||||||||
Pressure Reducing Valve | ✓ | ✓ | |||||||||||||||||||||||||
Flow Switch | - | ✓ | |||||||||||||||||||||||||
Flow Transmitter (4-20mA) | - | ✓ | |||||||||||||||||||||||||
Sludge Hopper Level | - | ✓ | |||||||||||||||||||||||||
Remote Monitoring & Control Capabilities | - | ✓ |
Disclaimer: We continuously update and improve our products and services, contact us for more detailed information or to confirm specifications. MAK Water takes no responsibility for any errors resulting from the use of information contained on this website.
Applications
Real-world examples
Schlumberger, one of the world’s leading providers of technology for reservoir characterisation, drilling, production, and processing to the oil and gas industry, contacted MAK Water to design and manufacture a water recycling system for their new facility. Two separate equipment washbays, with differing waste streams, required two separately designed systems to achieve the strict treated water quality requirements. A customised Dissolved Air Flotation (DAF) plant was required for the main equipment washbay and a customised Multimedia Filtration (MMF) plant was required for the pressure test bay. A high level of plant customisation, technical capabilities and experience was required to achieve the complex treated water quality requirements.
Jandakot, Western Australia
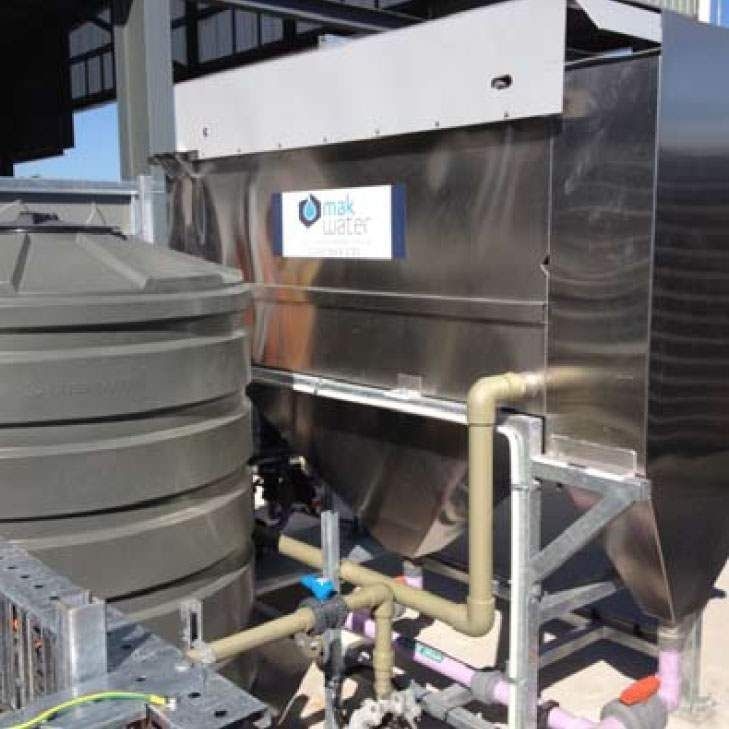
Wash Bay Wastewater Treatment for Train Support Facility
QR National (Queensland Rail National, now Aurizon Holdings) required a wastewater treatment solution, to treat effluent from the truck and container wash bay at their transport depot, to a standard complying with Brisbane City Council’s trade waste guidelines. As a renowned specialist in design and manufacture of wash bay wastewater treatment systems, MAK Water was engaged by QR National to design, manufacture, install and commission a plant, to treat 10,000 litres per day of combined truck and shipping container wash bay wastewater.
Hemmant, Queensland
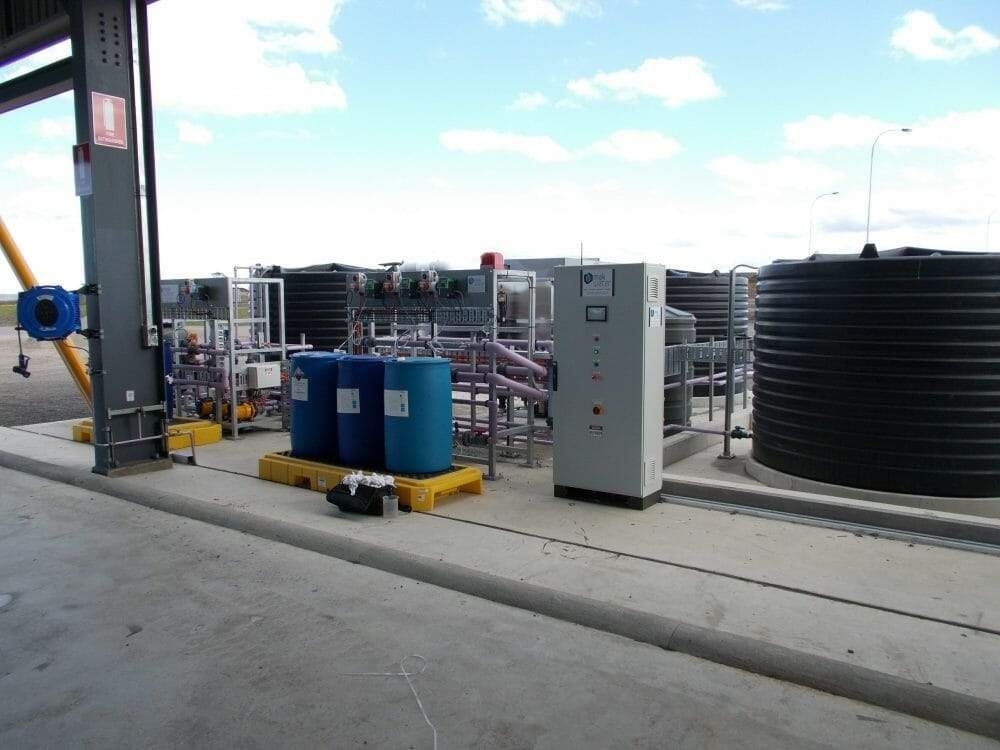
Trade Wastewater Treatment for Bakery
A bakery facility in Adelaide had wastewater from the baking process discharging into the local sewage network. The bakery needed to improve its trade wastewater treatment system in order to comply with the local authority discharge permits. MAK Water was commissioned to supply and install an onsite wastewater treatment plant. Suspended solids, biological oxygen demand (BOD), and oil and grease were the main contaminants that needed to be reduced through the treatment process.
Adelaide, South Australia
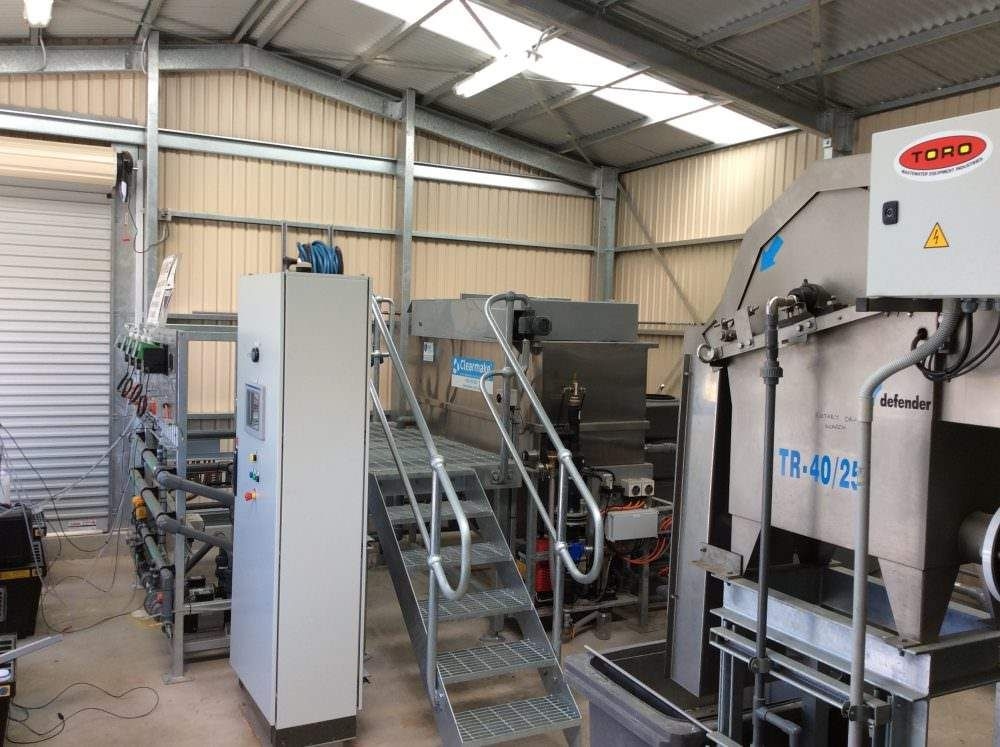
Wastewater Treatment for Abattoir
A large abattoir in New South Wales was having issues with their Dissolved Air Flotation (DAF) treatment plant that is used for removing tallow from their wastewater stream. Poor understanding of the operation of the DAF and little maintenance over the years had seen the asset and its components become blocked and damaged. The abattoir approached MAK Water to source replacement components for their plant that had been purchased from an overseas vendor and help to get the DAF operational again. MAK Water was selected as the preferred service provider because of its extensive experience with DAF plants in wastewater treatment applications and its ability to source the specialist components required.
New South Wales

As part of a facility upgrade, Hastings Deering required a new wash bay water recycling system at its Rockhampton facility. The wash down water was largely contaminated with dirt and soil, but there was also a small amount of oil and grease entrained in the wash down water that needed to be removed prior to re-use. Bench testing demonstrated that Dissolved Air Flotation (DAF) was the lowest cost solution.
Rockhampton, Queensland
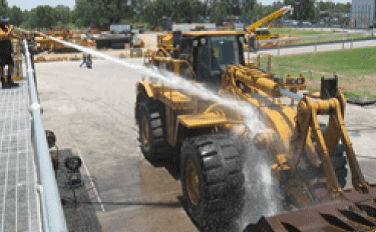
Wash Bay Wastewater Recycling for Defence Army Base
To maximise the efficiency of wash down operations at its Brisbane Barracks, the Department of Defence decided to consolidate 18 vehicle and equipment wash down stations into one facility. Key operational goals for the project included minimising town water consumption, reducing load on the sewerage treatment system and ensuring all relevant environmental and occupation health and safety requirements were met.
Enoggera, Queensland
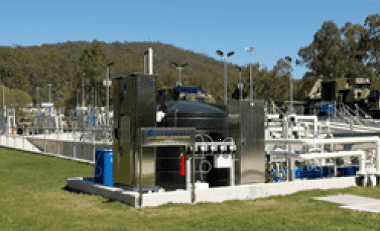
What people are saying
Degnan are very satisfied with the service offered by the MAK Water Team.
Andrew Bridson - Design Manager
Degnan
Water Clarification
Related Solutions
Gas Energy Mixing System
The Gas Energy Mixing (GEM®) System is an innovative and patented approach to wastewater treatment. The GEM System removes higher levels of contaminants than conventional dissolved air flotation (DAF) systems, using less chemicals, while generating significantly drier sludge.
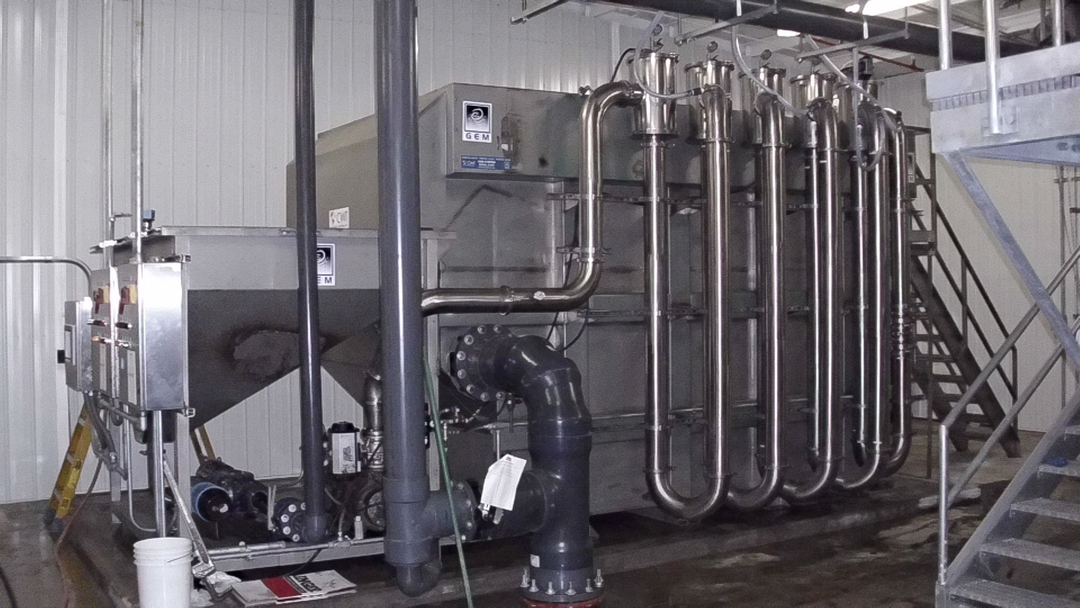
Gravity Clarification
MAK Water’s Clearmake™ range of Gravity Clarification (GC) systems are designed to clean water prior to reuse, or discharge to the sewer or the environment.
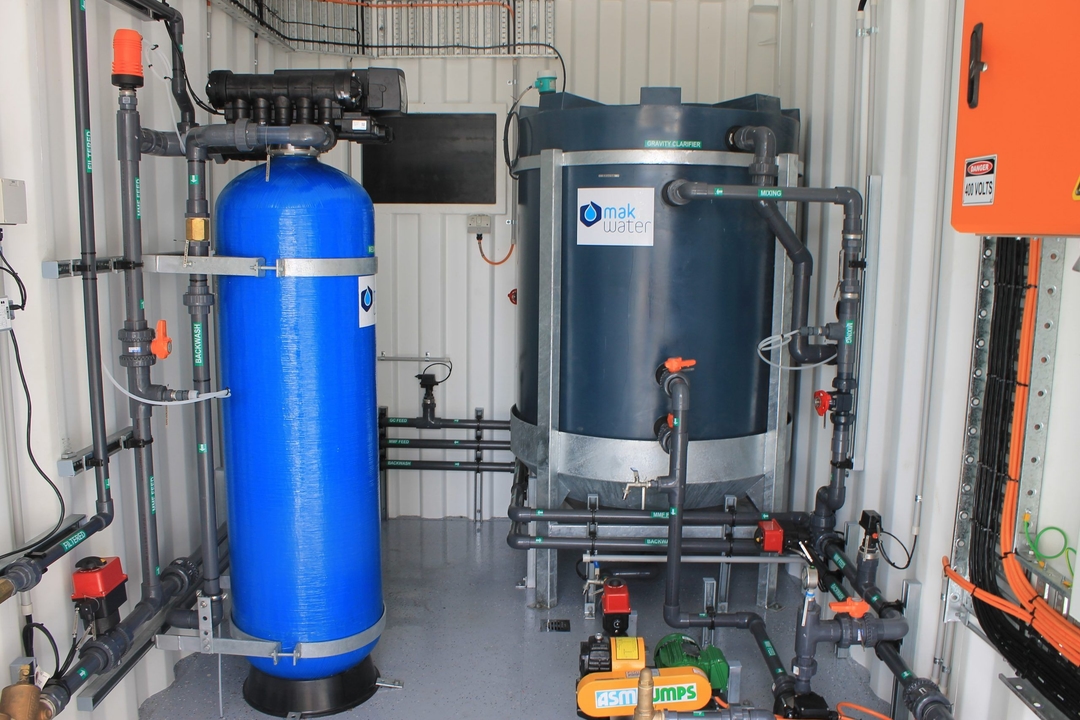
Lamella Clarifier
Lamella clarifiers can manage feed water with high concentration of suspended solids.
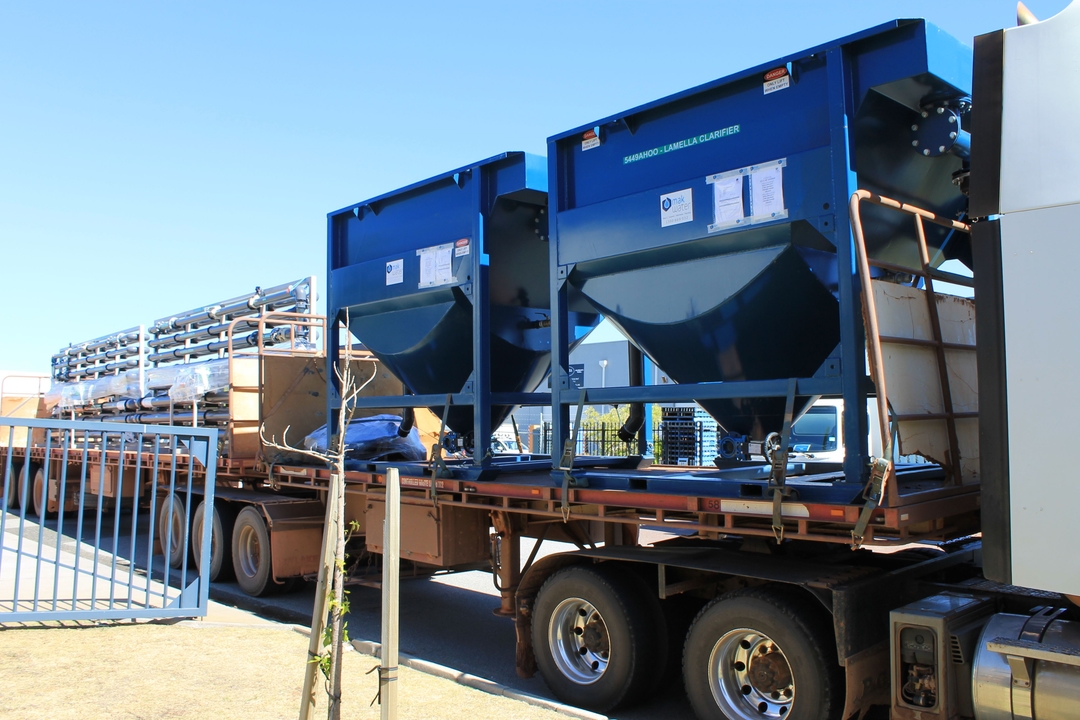
Oil Water Separators
MAK Water’s Clearmake™ oil and water separators remove free-floating hydrocarbons such as diesel, hydraulic fluid oil and heavy suspended solids from wastewater.
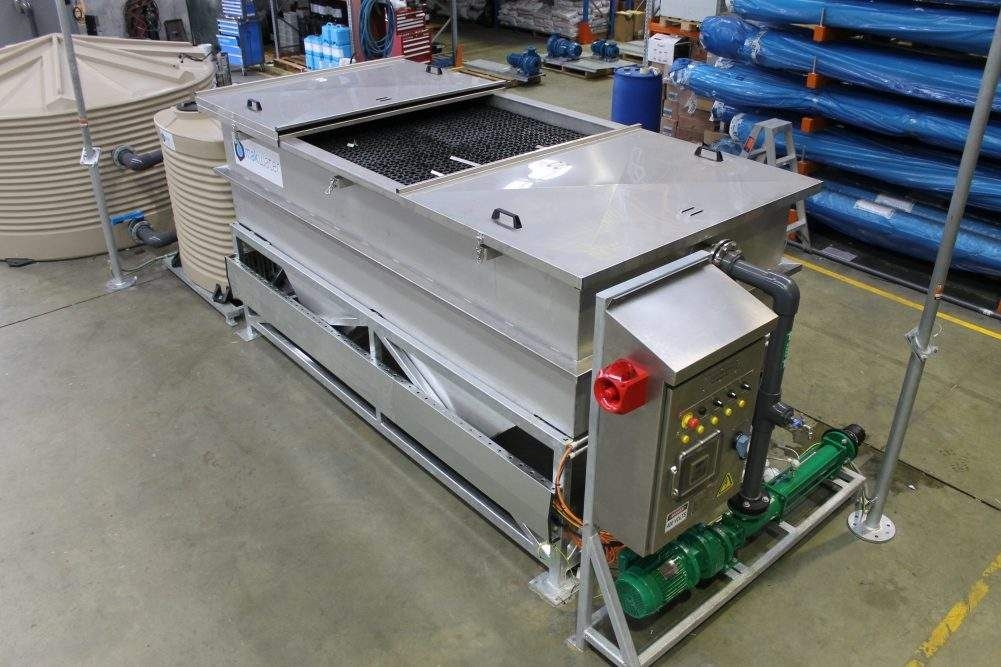
Pump Station
The Clearmake™ Pump Station is designed to transfer water to a local sewer connection or to a downstream treatment process cost-effectively when gravity cannot assist
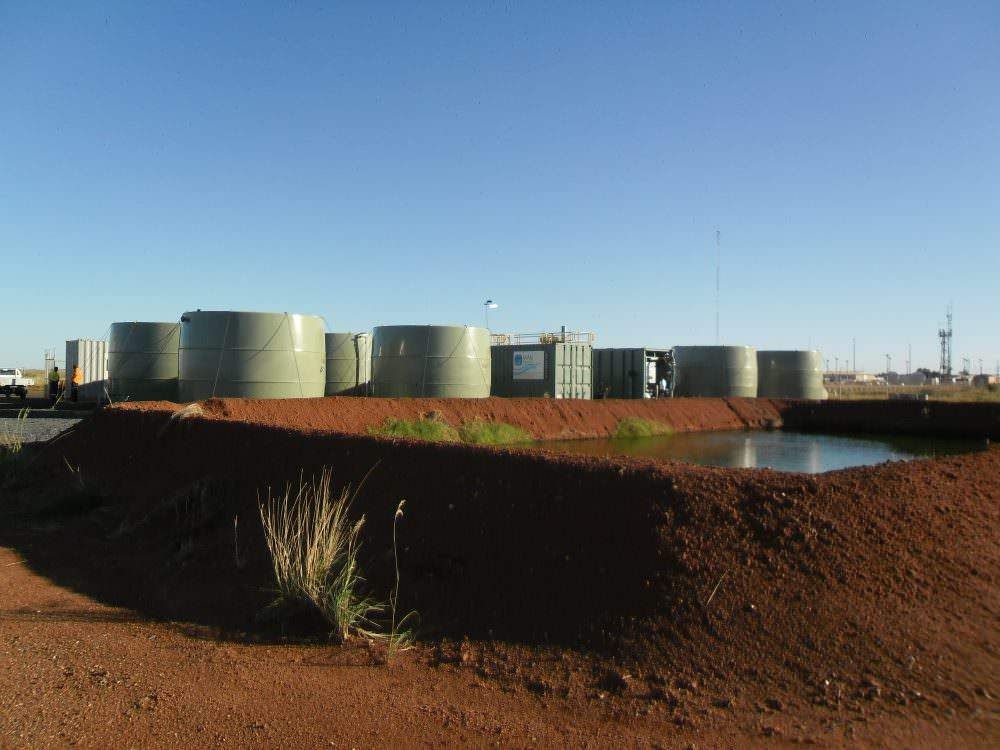