Screw Screen
The Screw Screen (Product ID: SS) is an effective solution for screening solids from raw sewage and industrial wastewater. Designed for installation in a concrete channel, this system is available with or without a compaction system, which is designed to reduce the weight and volume of captured screenings. The integrated compactor, located at the end of the transport section, efficiently washes, compacts and dewaters the screenings.
This innovative system offers low maintenance and requires minimal initial investment, making it a cost-effective option for wastewater treatment. The Screw Screen has a self-cleaning screen basket, with brushes fitted along the screw that continuously remove debris from the screen element surface, ensuring high solids removal efficiency. It can reduce the volume and weight of screenings by up to 50% after compaction. The transport section is available in either tubular or U-section designs, with flexible length options to suit various installation needs.
Key manufacturing features include a treatment capacity of up to 1,250 m³/h, which supports high-demand operations. The screen element is offered in two options: rounded holes ranging from 3 to 10 mm or wedge wire ranging from 0.25 to 3 mm. These customisable features makes the Screw Screen a trusted, efficient choice for screening raw sewage and industrial wastewater.
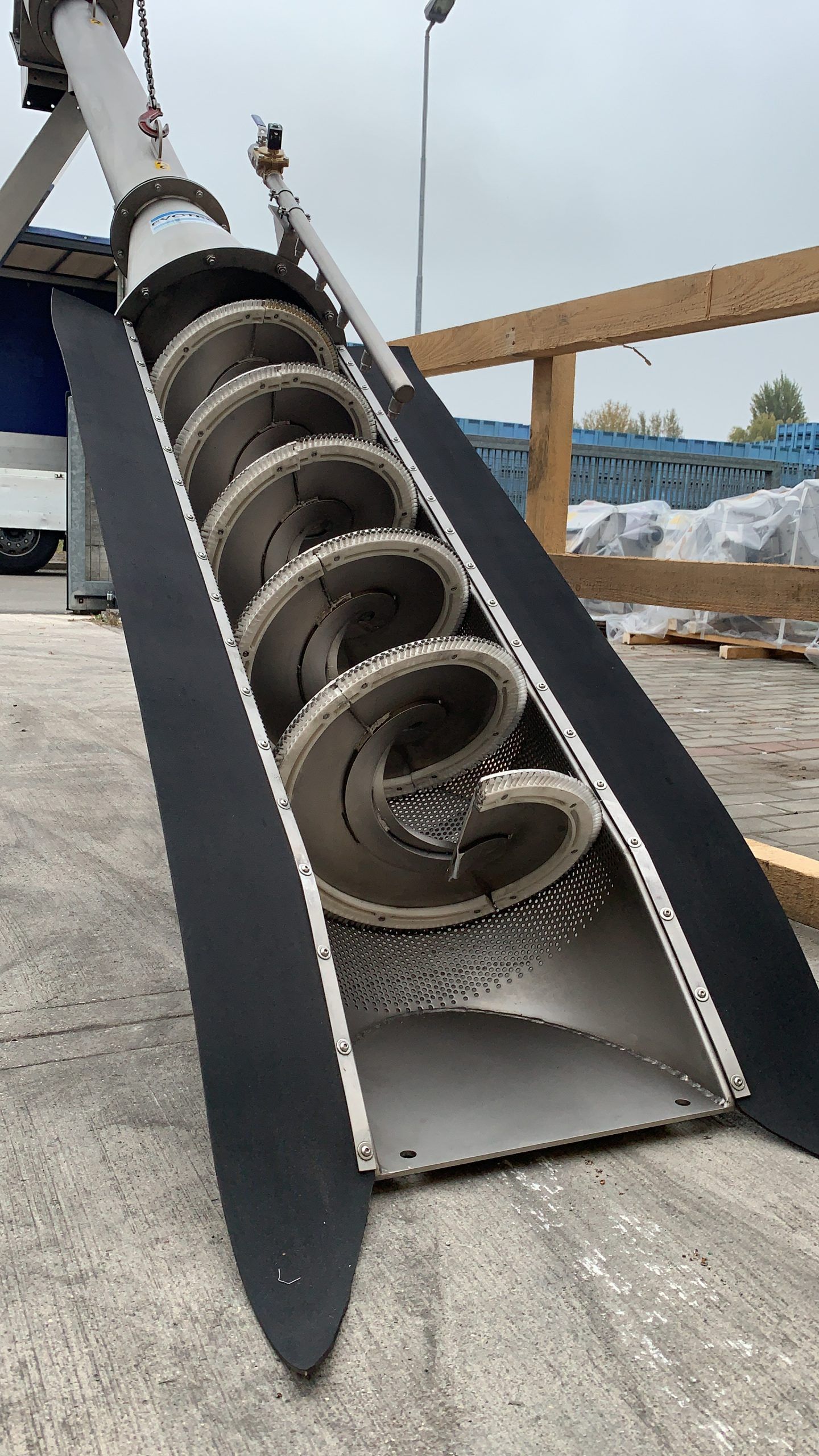
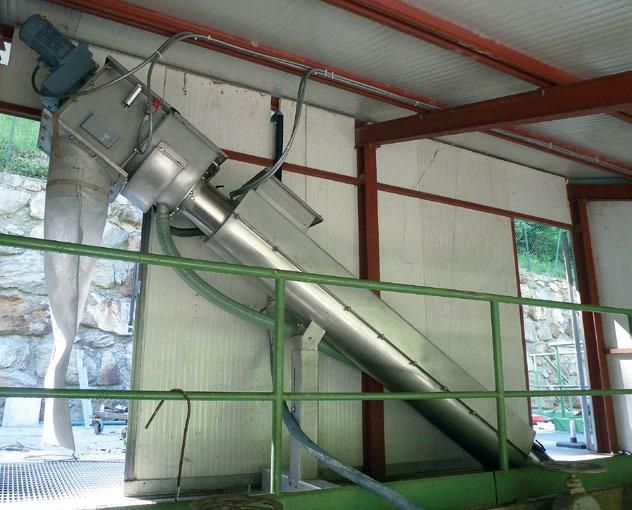
Technical Specifications
Standard Specifications
Parameter | Units | SS-mK-110 | SS-mK-160 | SS-mK-260 | SS-mK-390 | SS-mK-610 | SS-mK-830 | SS-mK-1000 | ||
---|---|---|---|---|---|---|---|---|---|---|
Treatment capacity*1 | With rounded holes (mm) | Ø3 | m3/h | 80 | 122 | 158 | 320 | 502 | 690 | 865 |
Ø4 | 93 | 137 | 218 | 360 | 528 | 756 | 920 | |||
Ø5*2 | 108 | 158 | 259 | 390 | 612 | 830 | 1,000 | |||
Ø6 | 126 | 164 | 288 | 430 | 630 | 850 | 1,070 | |||
Ø7 | 137 | 183 | 310 | 468 | 730 | 905 | 1,160 | |||
Ø10 | 158 | 194 | 333 | 495 | 790 | 970 | 1,250 | |||
With wedge wire (mm) | 0.25 | 17 | 34 | 75 | 115 | 180 | 220 | 290 | ||
0.5 | 45 | 64 | 95 | 170 | 300 | 340 | 385 | |||
1 | 50 | 81 | 135 | 252 | 350 | 430 | 590 | |||
2 | 85 | 100 | 145 | 303 | 430 | 580 | 785 | |||
3 | 112 | 125 | 187 | 340 | 505 | 730 | 900 | |||
Dimensions | W - Channel min/max | mm | 300/477 | 358/542 | 470/620 | 570/718 | 740/888 | 875/975 | 1,065/1,167 | |
H | 35˚ | 410 | 420 | 430 | 550 | 660 | 800 | 860 | ||
45˚ | 515 | 535 | 540 | 705 | 838 | 985 | 1,050 | |||
A*3 | 5,124 | 5,124 | 5,124 | 5,124 | 6,040 | 6,040 | 7,840 | |||
B | 4,075 | 3,975 | 4,044 | 3,990 | 4,512 | 4,510 | 4,680 | |||
C | 3,040 | 2,990 | 3,035 | 2,980 | 3,735 | 3,770 | 3,650 | |||
D | 800 | 800 | 800 | 800 | 1,000 | 1,000 | 1,000 | |||
S | 1,500 | 1,500 | 1,500 | 1,500 | 1,500 | 1,500 | 1,500 | |||
Installed motor power | kW | 0.75 | 0.75 | 0.75 | 0.75 | 0.75 | 0.75 | 1.1 | ||
Screw gear reducer speed | rpm | 11 | 11 | 11 | 11 | 8 | 8 | 8 | ||
Washwater Screen basket / compaction zone (at 3 bar) | L/min | 23/31 | 23/31 | 23/31 | 23/31 | 62/44 | 62/44 | 78/56 | ||
Empty weight (standard length) | kg | 300 | 318 | 325 | 350 | 608 | 642 | 1,100 |
*1Theoretical, calculated using clean water, *2Standard screen type & aperture, *3Transport section can be lengthened or shortened, which will affect other dimensions.
Standard Inclusions and Options
Equipment | Standard Supply | Optional Supply | ||
---|---|---|---|---|
Screw screen | Rounded holes screen element | Ø5mm aperture | ✓ | - |
Custom aperture (3, 4, 5, 6 ,7 or 10mm) | - | ✓ | ||
Wedge-wire screen element (0.25, 0.5, 1, 2 or 3mm) | - | ✓ | ||
Integrated screenings compaction (can be deleted as an option) | ✓ | - | ||
Screen basket cleaning, bolted nylon brushes | ✓ | - | ||
PE pipe for returning liquid from compaction zone | ✓ | - | ||
Squared outlet spout | ✓ | - | ||
Bolted screenings compaction system cover | ✓ | - | ||
Lifting eyebolts | ✓ | - | ||
Nord drives with compact motor gearbox and cover guard | ✓ | - | ||
Machine carpentry, drive guard and anti-wear materials on screw | SS304, bolts A2 | ✓ | - | |
SS316, bolts A4 (recommended for coastal and corrosive environments) | - | ✓ | ||
Screw | High-carbon steel painted | ✓ | - | |
SS316L | ✓ | - | ||
Lengthen or shorten the standard screw transport section | - | ✓ | ||
Washing | Compaction zone only, with ½” manual valve | ✓ | - | |
Compaction zone with ½” manual valve and screening basket with 1” manual valve | - | ✓ | ||
Manifold for compaction zone and screening basket, with 1” manual valve | - | ✓ | ||
Automatic Longopac bagging system for screenings with 1x 80m long bag | - | ✓ | ||
Drive motor premium efficiency | IP55 | ✓ | - | |
IP65 with thermistor overload protection | - | ✓ | ||
Surface treatments*1 | ✓ | - |
*1 Stainless steel parts: stripping with acid solution, passivation with glass particles, final surfaces cleaning with anti-dust oil. Carbon steel parts: sandblasting SA 2.5 for external anti-rust paint RAL 5015
Instrumentation & Controls | Standard Supply | Optional Supply | |
---|---|---|---|
Safety limit switch for compaction zone opening hatch | - | ✓ | |
Level sensor, supplied loose for channel installation | Conductive probe | - | ✓ |
Ultrasonic | - | ✓ | |
Solenoid valve kit(s) for selected washing system(s) 24VDC | - | ✓ | |
Mechanical over-torque protection (backlash free-ball model) | - | ✓ | |
Control panel to AS/NZ 3000, for external installation | - | ✓ |
Disclaimer: We continuously update and improve our products and services, contact us for more detailed information or to confirm specifications. MAK Water takes no responsibility for any errors resulting from the use of information contained on this website.
Applications
Real-world examples
A northern NSW regional Council was seeking to upgrade their sewage treatment plant inlet works by replacing an old step screen that reached end of life. The Council was initially seeking a like for like replacement, however, wanted better removal efficiency and a solution that required minimal maintenance and operator input in day-to-day use. Key requirements included the ability to retrofit the new screen into the existing concrete channel to minimise site modifications, and incorporated screenings compaction and washing.
New South Wales
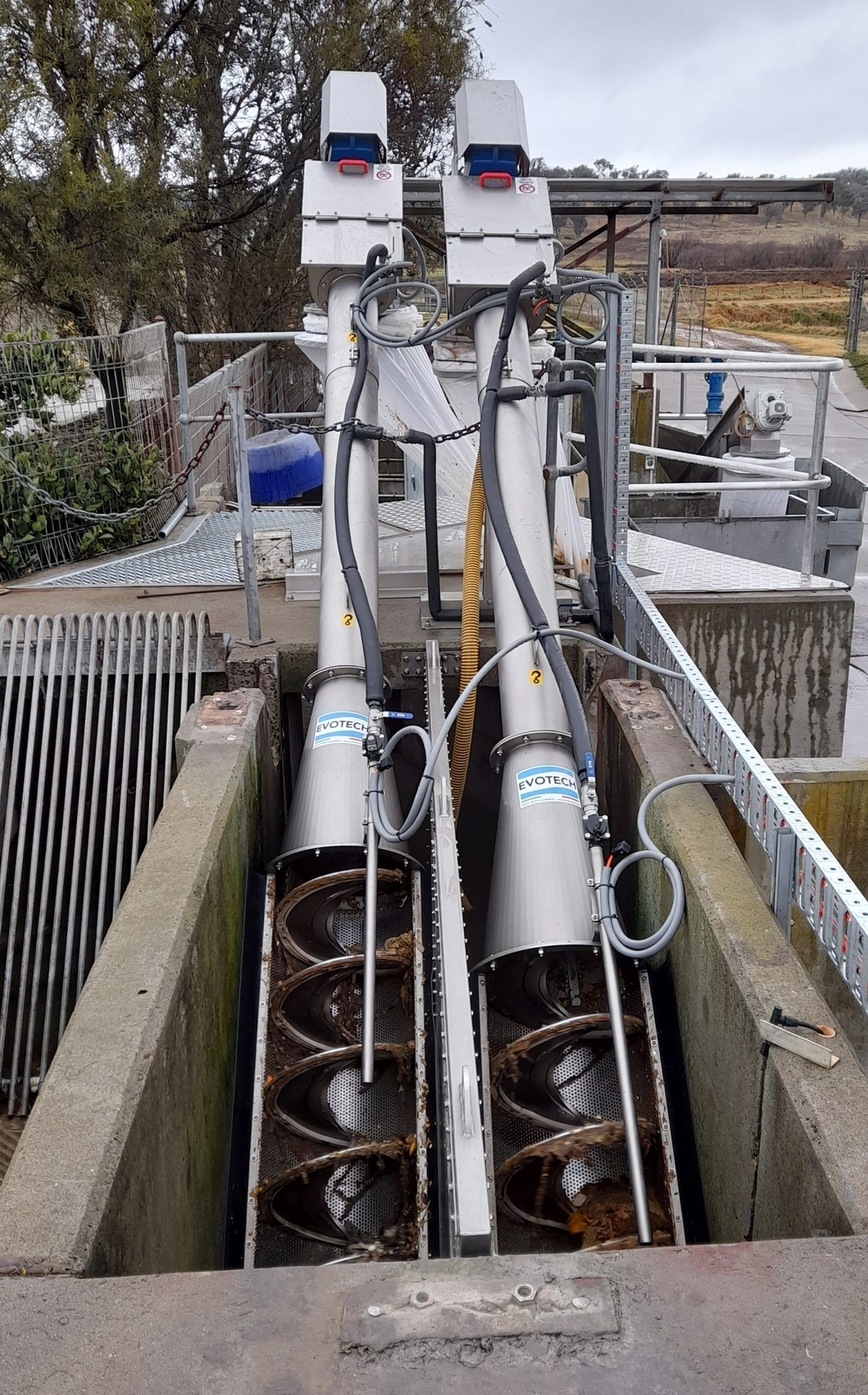
Inlet Screening for Pet Food Manufacturer
A pet food manufacturing facility in Western Sydney wanted to replace an ageing rotary drum screen due to poor screening performance leading to issues with a Dissolved Air Floatation process downstream. They also wanted to replace an existing screenings Screw Compactor that did not provide sufficient dewatering and used too much potable water for washing. MAK Water was engaged to provide a solution. We delivered an integrated and compact replacement to fit into the existing plant room with minimum impact to operations.
New South Wales
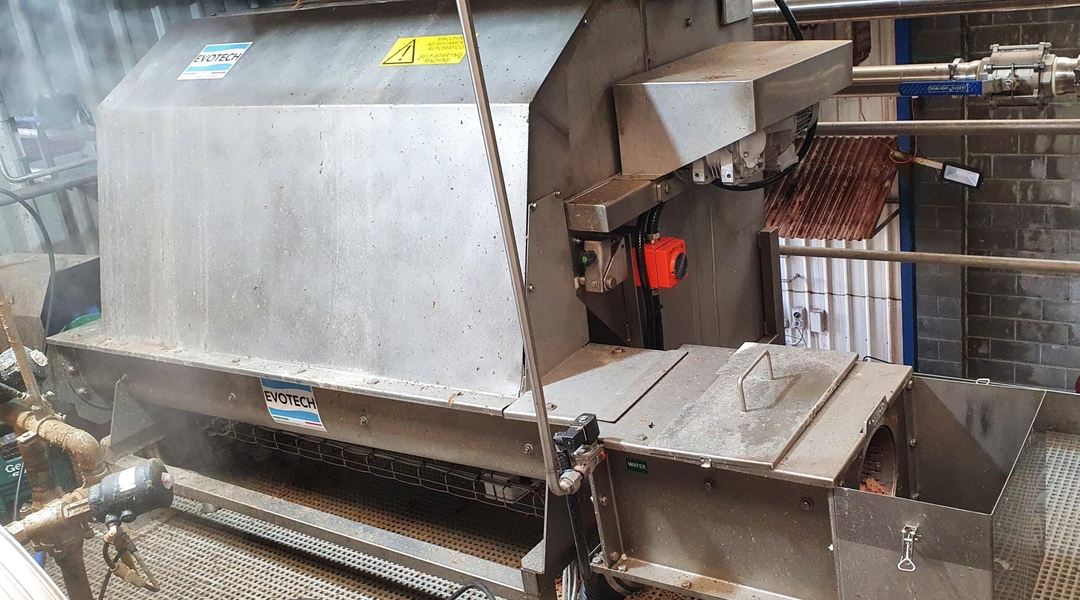
Screening & Grit Handling
Related Solutions
Compact Screen and Grit Removal Package
The Compact Screen and Grit Removal Package (Product ID: ICE) is a primary treatment machine that combines screening and grit removal in a single compact plant.
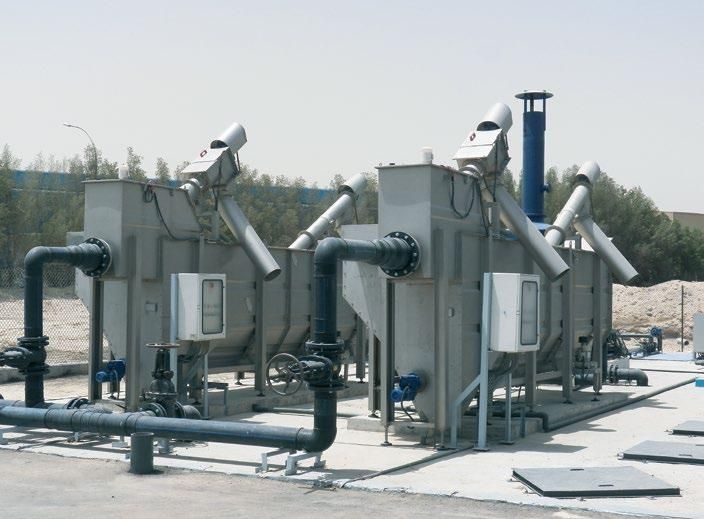
Compact Screw Screen
The Compact Screw Screen (Product ID: SSG) is an economical solution for screening of industrial wastewater or domestic sewage.
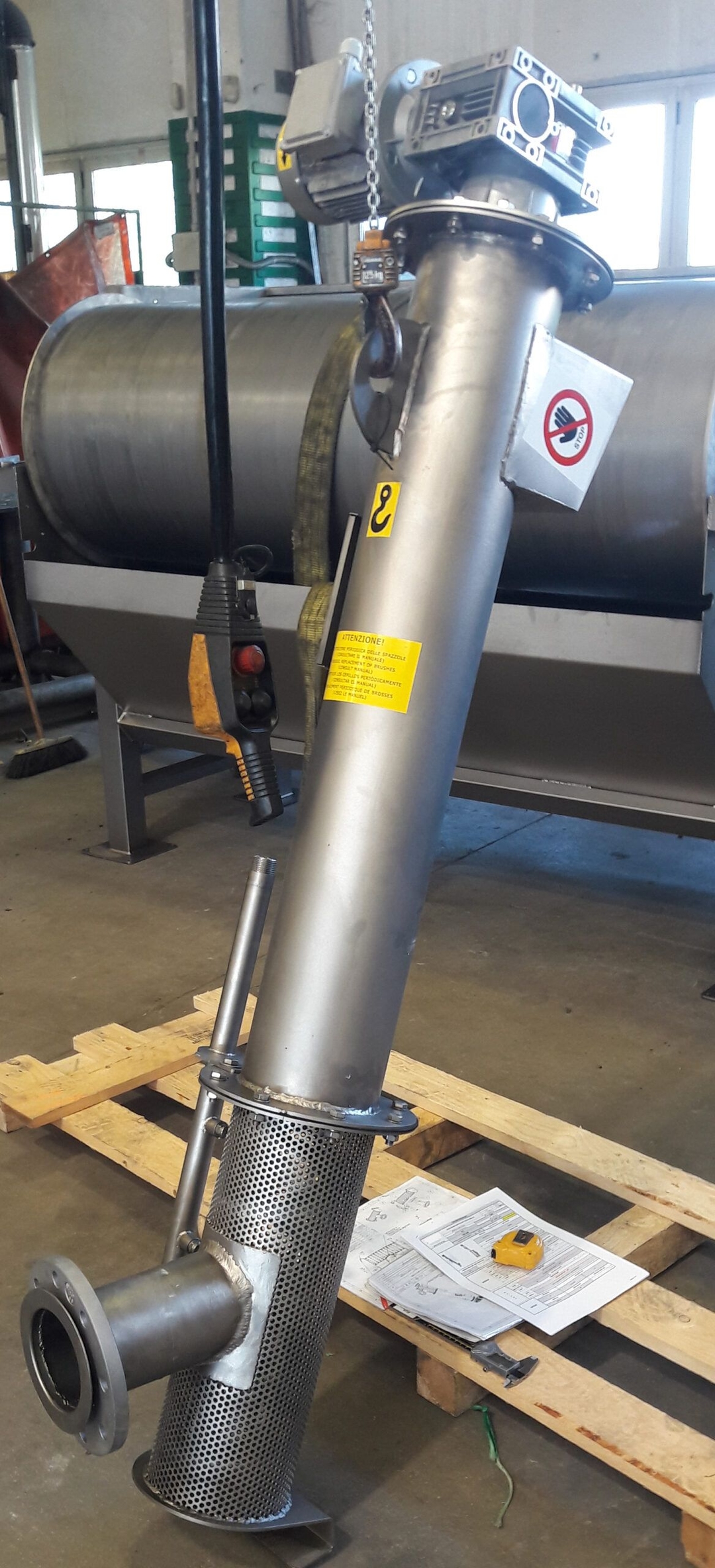
Grit Classifier
MAK Water’s Grit Classifier (Product ID: SAK) is used to separate grit (which can contain sand, gravel and other heavy solids) from municipal and industrial wastewater streams.
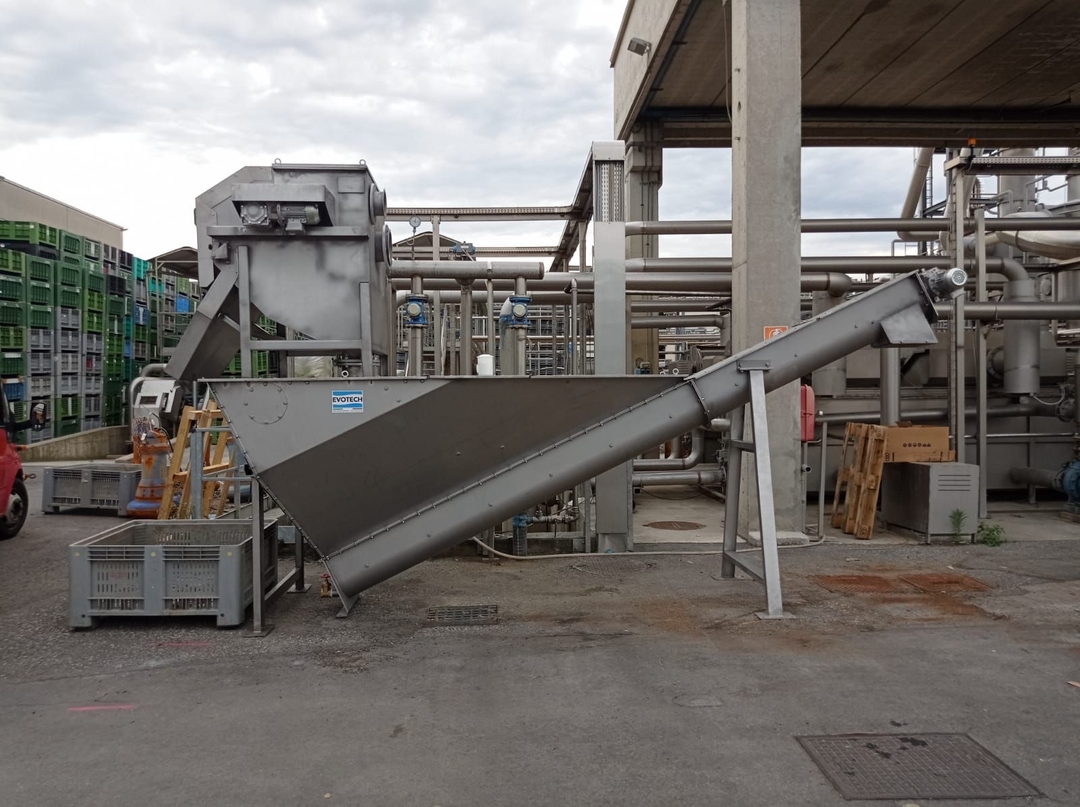
Grit Removal System
The Grit Removal System is designed to provide grit removal pre-treatment in a single packaged unit process.
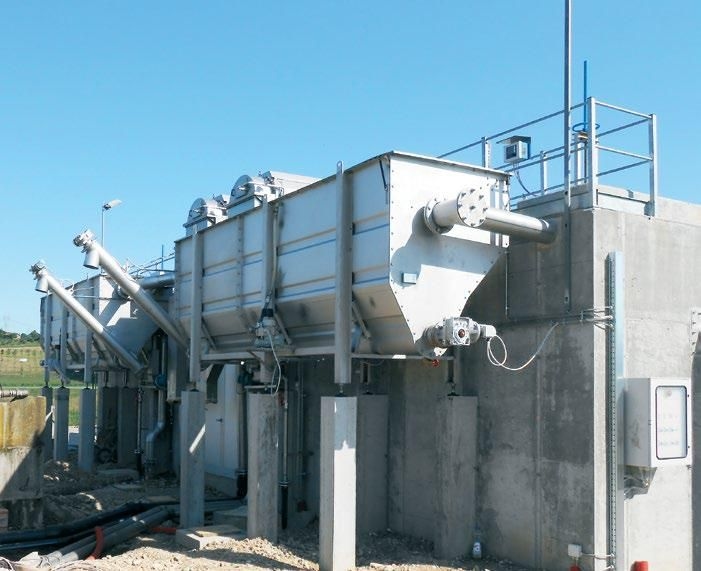
Internally Fed Drum Screen
The Internally Fed Drum Screen is a free-standing unit designed for separating settling solids from wastewater using an internally fed rotating drum screen.
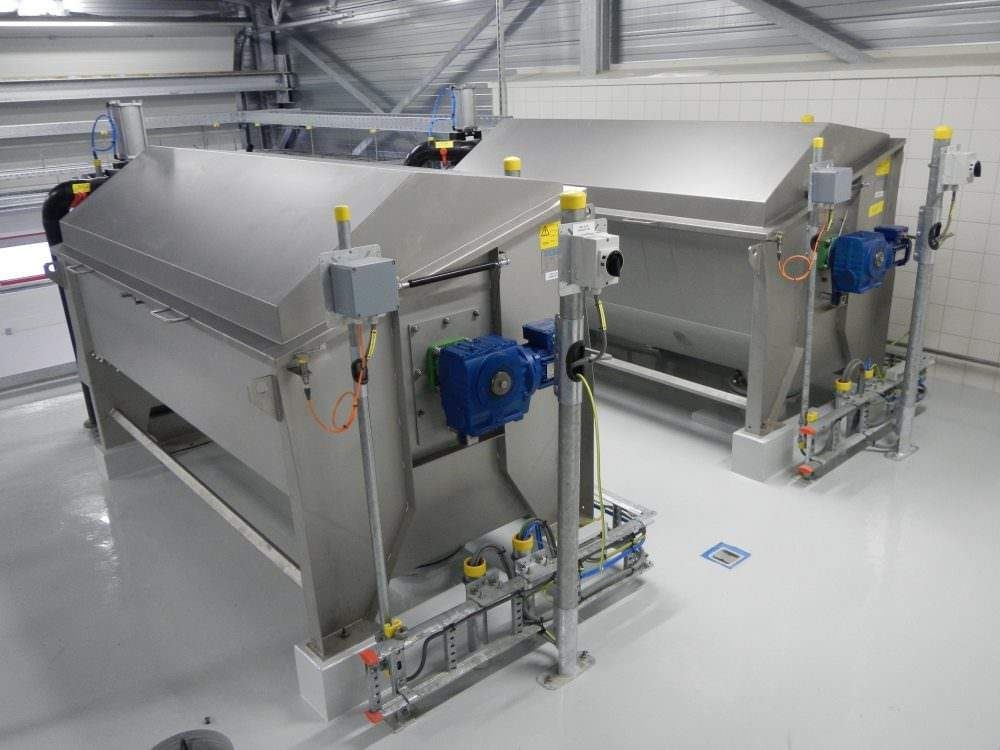
Rotary Drum Screen
The Rotary Drum Screen (Product ID: FTR) is designed to remove solids from industrial wastewater streams.
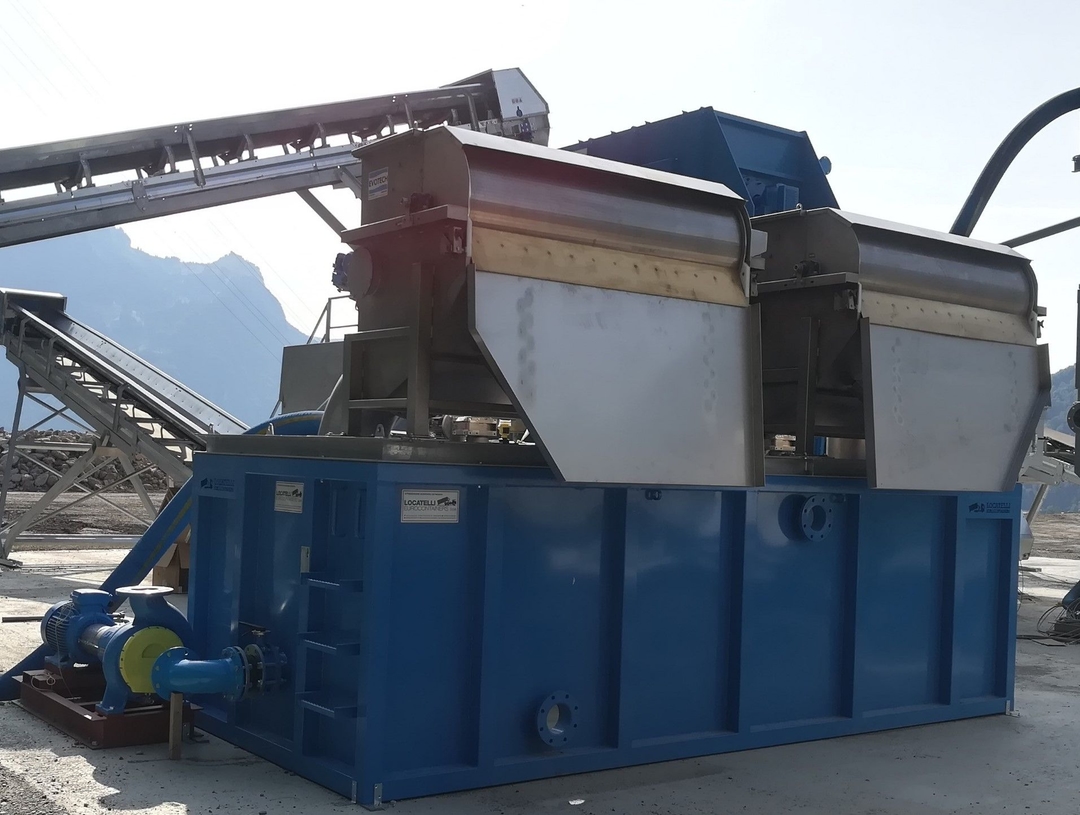